Our range of coilers and take up units are used to wind extruded products onto drums. For single product take up, the TU26 Traversing Take Up Unit is an ideal solution, with the unit traversing to allow neat layers of wound product.
The frame allows for varying drum sizes and the drive is carefully controlled to ensure coil quality is maintained.
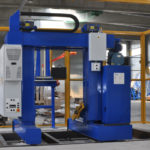
Holton Crest has designed and manufactured an automatic changeover twin coiler that is designed to continuously wind wire produced on a Holton Crest machine into open coils without any interruption in production speed.
The unit consists of two horizontally mounted expanding mandrels. When the required coil size has been wound, the wire is sheared from that coil and automatically hooked onto the other mandrel to start producing the next coil.
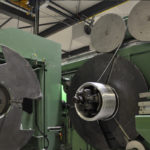
Holton Crest machines can accept a wide range of different feedstocks, from cast bar to rod and granular particle feed. We provide a range of different payoff methods to ensure a smooth, fast payoff whilst supporting your individual requirements, including:
Rotary Payoff - Includes a payoff turntable for accommodating continuously cast copper or aluminium rod feedstock.
Automatic Vertical Payoff - Allows for single or dual input configurations, with twin coils being automatically unwound vertically and straightened before entering the extruder, enabling precise control over feedstock preparation.
Particle Feed - Includes a particle hopper mounted on top of the extruder to allow for continuous feed of granular feedstock and controlled production.
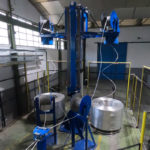
Product cooling is a key part of the continuous rotary extrusion process, minimising oxidisation and ensuring the high quality of the extruded product. The Holton Crest cooling unit consists of a free standing tank and cooling trough.
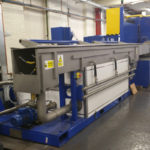